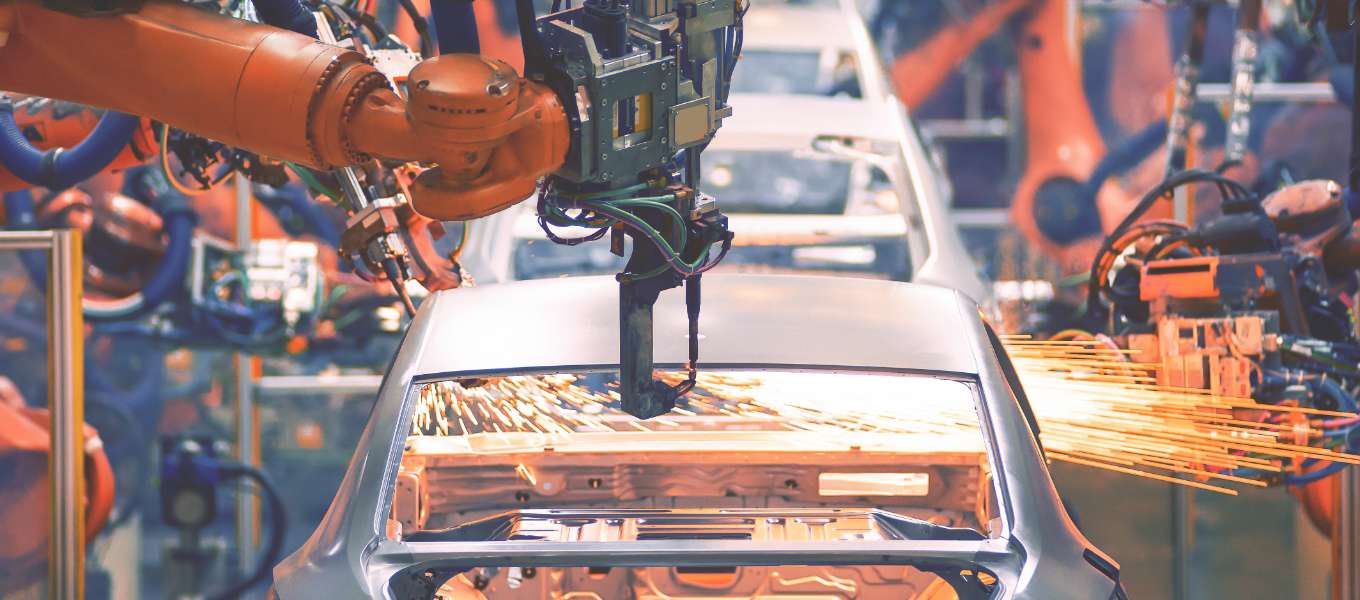
Frequently asked questions
To serve our customers better, we have listed some of the most frequently asked questions about our products, construction standards, and technical terminology.
LSF is short for low smoke and fumes compounds. They are used in applications where the cable is required to emit low smoke and produce no halogen acid gases in the event of a fire. With low smoke emission, the exit signs are clearly visible to people for escape; since it doesn’t contain halogens, the cable also won’t give off acidic gases when burning. The same compound is sometimes abbreviated as: LSZH – Low Smoke Zero Halogen; or LSOH - Low Smoke Zero Halogen.
LSF material does not contain halogen, but the test methodology has an accuracy of +/- 0.5% therefore the specification has this value.
Building wires are manufactured to BS 6004. For general use they are insulated with TI1 PVC insulation, which has an operating temperature of 70°C. In case higher operating temperatures and higher current carrying capacity is required, then type TI3 PVC insulation can be used with an operating temperature of 90°C. In the case of XL-LSF insulated building wire, the operating temperature is 90°C.
It is the bi-colour combination of green and yellow used for earthing. One of the colours covers at least 30% of the surface of the core, while the other colour covers the remainder of the surface.
The new colour schemes were adopted in British Standards to have a more recognisable code across Europe. It is not compulsory to change colours in the UAE.
Number of cores | Old core colours | New core colours |
---|---|---|
2 | Red, black | Brown, blue |
3 | Red, yellow, blue | Brown, black, grey |
4 | Red, yellow, blue, black | Brown, black, grey, blue |
The new colour schemes were adopted in British Standards to have a more recognisable code across Europe. It is not compulsory to change colours in the UAE.
U0 is the rated power frequency voltage between conductor and earth or metallic screen for which the cable is designed. U is the rated power frequency voltage between conductors for which the cable is designed. Um is the maximum value of the highest system voltage for which the equipment may be used (see IEC 60038).
There is no difference, both these voltage grades are same with highest system voltage Um = 12 kV. The XLPE insulation nominal thickness for cables with this voltage grade is 3.4 mm as per IEC 60502-2 (2005) as well as BS 6622 (2007) specifications. Hence the same cable may be termed as 6/10 kV voltage grade as per IEC 60502-2, or 6.35/11 kV voltage grade as per BS 6622.
Fire resistant cables manufactured by Ducab as per BS 7846 have special grade mica tape wrapping over the conductor. Mica as a mineral retains its insulation property even in case of extreme fire temperatures of up to 950°C. Mica tape over the conductor forms a tube when subjected to fire and provides a barrier to insulate the conductor and prevent short circuit. The areas of application for these cables include,
- Essential safety circuits for fire detection, fire alarms, etc.
- Power supply to equipment used in firefighting, like sprinkler pumps, and smoke extractors
- Services where circuit integrity is very important in a fire, like special equipment in hospitals
The minimum bending radius of cable is that radius below which the cables should never be bent. The minimum bending radius depends upon the type, voltage grade, and construction of the cable. This value is provided wherever required by the customer. Wherever possible, a generous bending radius should be used.
Cables are supplied on the drums and are used only for transporting the cable from one place to other. Bending on the drum is carried out under controlled conditions in the manufacturing plant.
Type tests are made before supplying a type of cable, to demonstrate satisfactory performance characteristics to meet the intended application. Once these tests have been made they don’t need to be repeated, unless changes are made in cable materials or design or manufacturing process, which might change the performance characteristics.
When type tests have been successfully performed on a type of cable with a specific conductor cross sectional area and rated voltage, the type approval is accepted as valid for cables of the same type with other conductor cross sectional areas and/or rated voltages subject to satisfaction of conditions set out in the IEC specification.
Material | Key properties | Recommended for |
---|---|---|
PE | High mechanical strength | Direct burial and duct installation |
PVC | Flexibility and flame retardance | General purpose |
LSF | Zero halogen, low smoke | Mass transit systems, high rise buildings, public areas and confined locations |
LSF is for applications requiring low smoke and fumes, whereas graphite, being carbon, burns easily and generates smoke, which is contradictory to LSF. Hence LSF cables are not offered with graphite coating.
Graphite coating is applied to cables to enable electrical testing of the outer sheath. If it is important for the outer sheath to pass such a test, we will always recommend PE as the sheath material. PE has a higher electrical strength than PVC and is much more resistant to moisture. Moisture can more easily penetrate PVC and degrade the electrical strength.
For all cables in service, during load cycles there is expansion and contraction of the cores. The copper wires cannot expand to the extent of XLPE insulation. Hence there is a chance of the copper being pushed into the insulation. The semi-conductive bedding tape provides a cushion and protects the core surface from damage.
There are three main properties
- Oxygen index of more than 30
- Halogen (acid gas) content of less than 20%
- Mechanical and electrical properties to meet requirements of Type 9 of BS:7655
Polymers, especially Polyethylene, are known to be susceptible to UV radiation. Exposure for a prolonged duration may result in surface-cracks developing. Which is why we add a special UV radiation resistant stabiliser package to our insulation materials, to protect the insulation from deterioration.
Maintaining minimum dimensions of any specification when manufacturing cables depends on two factors:
- Quality of material: excellent insulating grades have very high dielectric strength, and the conductivity of electrolytic grade copper is much higher than commercial grade copper
- Manufacturing technique: for example, high process capability indicates stricter tolerances, eccentricity of insulation allowed is less than 10%
Our cables excel on both counts, so they are manufactured at optimum dimensions, which makes the cable slimmer, uses less material, and at the same time makes them more efficient.
C-W-Z tests are referenced in BS: 6387 and are required by cable standards such as BS: 7846. These letters refer to standards of fire resistance
- C – Test with fire only
- W – Test with fire and water spray
- Z - Test with fire and mechanical shock applied simultaneously during burning
To meet the C category the cable must maintain circuit integrity while subjected to fire at 950°C for three hours. To check the W category, the cable is sprayed with water while also subjected to fire, to simulate the effect of an activated sprinkler system. In the Z category, the cable is subjected to mechanical shocks during the fire test to simulate falling debris. During all these tests the cable carries electricity at rated voltage. These tests are significant as they simulate the fire conditions under which the fire-resistant cables are expected to perform.
Ducab recommends RP-PVC for jacketing of cables, which are not going to be used in areas of high population density, but still have a critical requirement for reduced fire propagation.
Yes, we issue special instructions which detail the conditions to be observed during the storage and installation of LSF cables.
Cable installation under shade is essential to prevent heating by direct sunlight. Heating from the ambient conditions will reduce the current rating adversely as the cable will reach its maximum temperature even when carrying a reduced load.
If the cable is installed following the best practices and not overloaded, then the expected service life of a MV cable is more than 25 years.
We would need a clear statement about the required load, system voltage, route length, installation conditions, environment (thermal resistivity of soil or air temperature, etc.), number of circuits, distance between two circuits, earth fault current, and 3-phase short circuit current.
Discharges in a cable are caused by the breakdown of the gas contained within voids in the insulation. These tiny electrical discharges release electrical charges, which can be detected using highly sensitive equipment. The voltage at which the breakdown first occurs is known as the discharge inception voltage and the charge is measured in picoCoulombs (pC). These discharges can lead to cable failure in service, so it is vital to detect them during routine tests of each cable length. Specifications for MV polymeric cable all require measurement of partial discharge and define the maximum level of discharge acceptable at particular test voltages. However, any discharges detected within a cable should be identified and eliminated even if found to be below the specification limit. However, any discharges detected within a cable should be identified and eliminated even if found to be below the specification limit.
Installation and commissioning tests for any cables are not done by Ducab. We recommend that contractors follow IEC recommendations.
The sheath test can only be carried out on cables with a semi-conductive coating on the outer sheath.
Using AC test equipment for onsite testing of MV cables is not cost effective. The DC site test has been used for many years, but some research suggests that it is not completely effective and, in some cases, may cause harm to polymeric cables. VLF testing is an alternative method, which is based on AC testing, but it is carried out at a very low frequency (VLF). By generating very low frequency (VLF) down to 0.1 Hz (instead of power frequency), it is possible to reduce the required power for charging the cable capacitance.
No. Ducab does not carry out any tests onsite.
Cables produced by Ducab are meant for distribution networks and industrial installations, they are not designed for submarine applications.