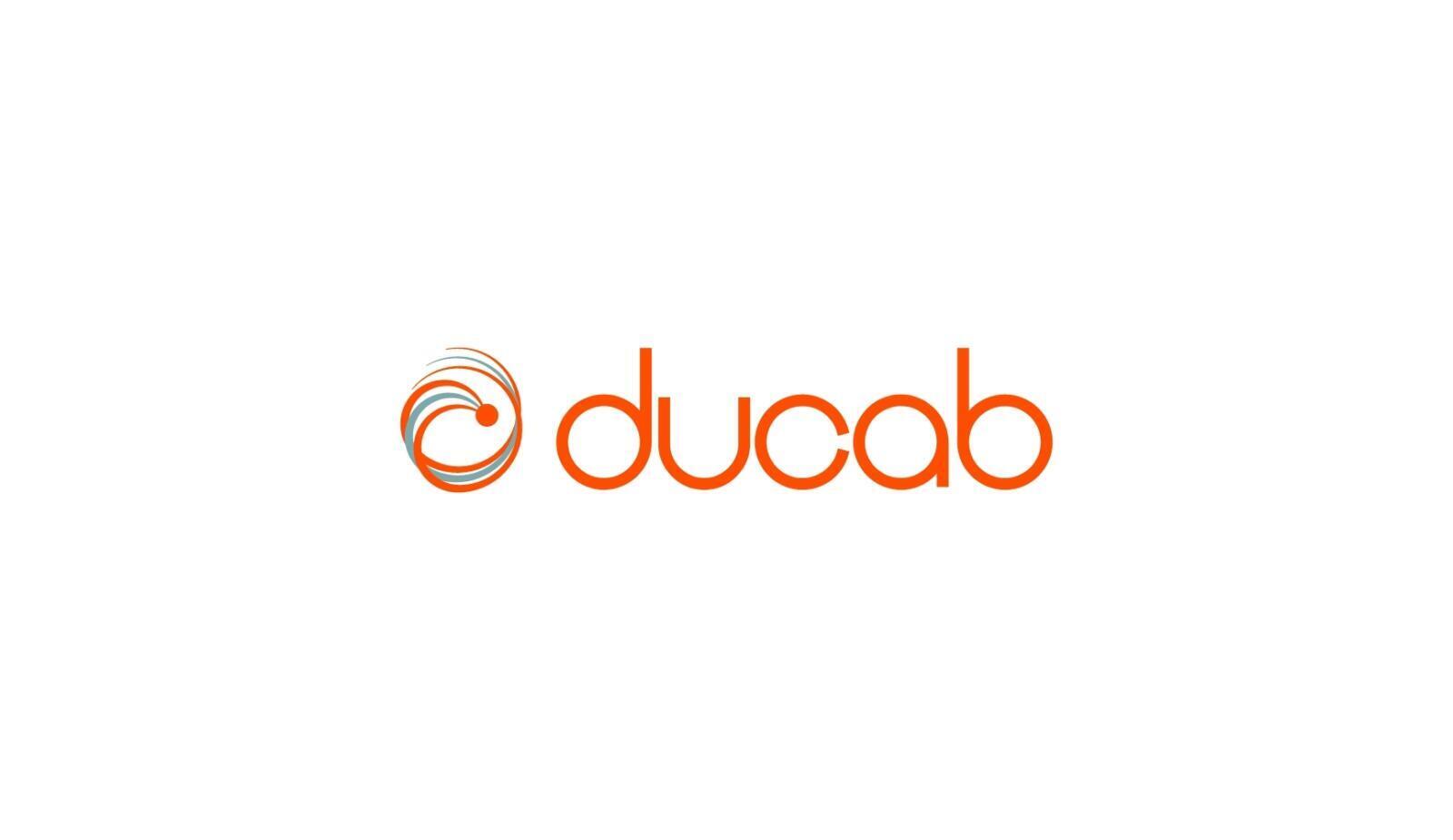
Power cables and thermal insulation: Ducab’s sustainability-first approach
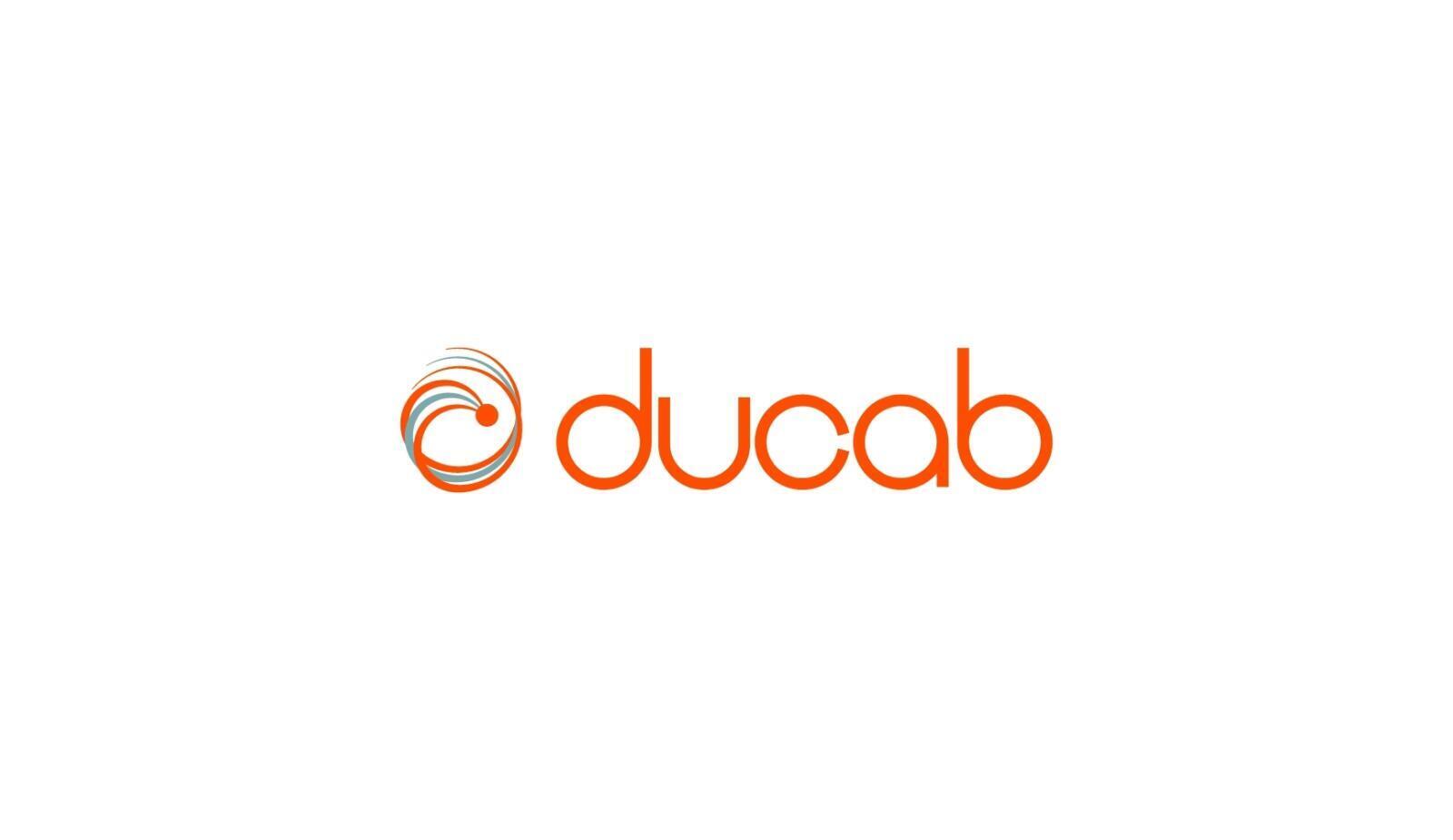
Our world has come a remarkably long way in the past couple of decades. Technology is transforming everything we know at an increasingly rapid pace – everything we do now is automated, hi-tech, smart, and hyperconnected. And with growing consumer demand for advanced solutions to their everyday tasks, energy needs grew in parallel, and with that, the demand for wires and cables that underpin the entire tech sector skyrocketed.
Indeed, the global power cable market was valued at a whopping USD148.6 billion in 2021 and is projected to reach USD277.8 billion by 2031.[1] As one of the biggest end-to-end solutions providers and manufacturing firms in the UAE, and a leading provider of renewable power solutions in the region and around the world, Ducab produces 150 different types of cables, including nuclear, solar, and flexible cables. Every year, the Group makes 13 million km of wires and cables, which is equivalent to 34 times the distance between Earth and the moon. In 2021 alone, the company manufactured 78,146 tons of cables and recorded annual sales of USD1.5 billion.[2]
However, with that remarkable manufacturing power came a tremendous responsibility. Ducab Group has always sought to minimise its ecological footprint and, over the years, embedded sustainable practices deep into its operations. This included everything from developing energy-efficient products and fire-resistant cables with low emissions of smoke and corrosive gases, to supplying specialised connectivity for renewable energy, in line with the UAE Net Zero by 2050 strategic initiative, which strives for net-zero emissions by 2050.
At Ducab, sustainability begins from the very start of the manufacturing process. The company has two grid-connected Solar PV plants – one on the ground and the other rooftop-mounted, with capacities of 2052kWp and 45.60kWp, respectively, which makes them capable of meeting some of the company’s requirements at the Jebel Ali factory and head office. This helps offset 13.76% of electricity consumption and saves 660 tons of CO2 emissions per year.
Another area where Ducab has succeeded in minimising its ecological footprint is the reuse and recycling of scrap material from the manufacturing process. The Group implements lean manufacturing principles in all of its operations in an effort to optimise the use of resources, monitoring material consumption using the ‘traffic light system’ (red/amber/green) to report material overconsumption at manufacturing stations.
Copper cable granulators allow for 100% recovery of copper from cables for recycling. Ultimately, a totality of the copper and aluminium the company uses – which are the primary material used in producing electric cables – are recycled. The Group has also instituted buy-back arrangements with customers for reuse of metal and wooden drums, as well as cable scrap, in an effort to improve the circular economy. Add to that the fact that the expected service life of a Ducab-produced MV cable is more than 25 years, greatly reducing the waste generated in the first place. Furthermore, purged PVC and Low Smoke Fume (LSF) head waste from extruders is recycled, and granulators placed on PVC/LSF extruders ensure inline recycling as the waste is produced.
Another advanced process is the “hot metal road”, a liquid metal transfer facility that can transport molten metal via overhead crane to preheated 14.5-tonne crucibles designed to keep metal in a liquid state for up to 18 hours at temperatures of 780°C. This, in turn, significantly reduces re-melting costs and helps save energy used in the re-melting process.[3]
In the UAE, Emirates Global Aluminium’s (EGA) Al Taweelah smelter began delivering molten aluminium to its customers back in 2016, becoming the first system in the UAE to link separate industrial sites. And Ducab Aluminium Company, which produces aluminium electrical wires, was the first customer to receive a delivery via EGA’s hot metal road.[4]
That said, the cable industry has many more breakthroughs in terms of bringing resource-efficiency into the manufacturing process and reducing the carbon footprint from their operations. “Green wires” are one example, where the conductor used is crafted from 99.97% pure electrolytic grade copper, which increases the current carrying capacity of the wire by up to 20%. The wires come with heat-retardant thermal insulation with a major component of Type C PVC compound, and with heat being the major source of energy loss from electrical wirings, green wires help reduce energy waste by up to 20%.[5]
With technology advancing at an increasingly rapid pace, sustainability must be prioritised at every step in the value chain, not only with the end user. Cables and other equipment are bound to become ever more ubiquitous, and manufacturers must work to reduce their carbon footprint at every step. With its pioneering projects and commitment to cutting emissions and waste, Ducab Group is a trailblazer and a pioneer in that regard, and as the world grows ever more connected, the Group will continue evolving in tandem, adapting to the requirements of the time every step of the way.